National Farmers stepped in and saved us in the spring of 2020
By Denise Rackley
Milking 800 cows three times a day doesn’t leave much room for change. In 2020, when the dairy processing plant decided it couldn’t haul the 65,000 pounds of Double Dale milk produced daily, Dan Rossiter thought it might be the end. “Thankfully, NFO was there to enable us to continue doing what we enjoy,” said Rossiter. While the world shuttered due to the pandemic, the Rossiters were looking toward a bright future.
Dan and Sharon moved to Ellisberg, New York, from Connecticut some 40 years ago to continue the dairy farming tradition passed down in Sharon’s family. Just a few miles east of Lake Ontario, winters can be challenging. “Lake effect snow storms can be a problem, but the cattle enjoy cooler summers.” While the dairy might be a bit far north for some, the Rossiters don’t mind. “We are able to grow 100-day corn and good alfalfa for the cattle,” Rossiter commented.
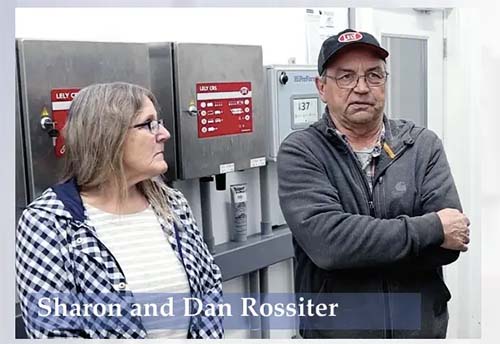
“Building from the ground up enabled us to explore lots of options,” said Pete Lorusso, herdsman and the Rossiter’s nephew. Cow comfort is the primary goal, followed closely by product quality and efficiency. A new free-stall barn with eight Lely robotic milkers was built to house up to 480 cows. The freeflow design and abundant monitoring of each cow and the entire barn made the Lely system the right choice for the Double Dale Dairy.
Automatic temperature controls abound – curtains, sprinkler system, and over 100 variable speed fans maintain optimal air quality while ensuring the cattle are comfortable. The robots are in the center, kept warmed by the cattle. An abundance of space, outward-facing feeding alleys, and sawdust-bedded mattresses round out the features of the new barn.
The cows are divided into four groups, two robots per group, so each robot serves about 60 cows. Pretty much everything is automated with the computer system monitoring and recording many benchmarks from the temperature of individual cattle to her ruminations and activity.
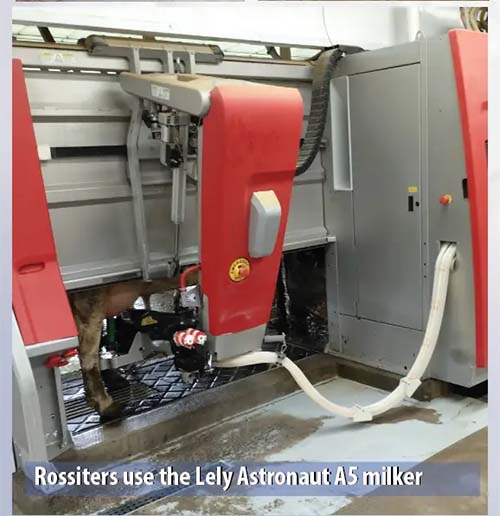
On average, the cattle are milked three times a day. However, since the cows enter the robot as they please, some are milked more, others less, Lorusso explained. Interestingly cows at the start of their lactation often enter the robot more often, some six to seven times a day. Cows at the end of their lactation may choose to enter only once a day.
When heifers first enter the new barn, there is some hands-on training needed. “We go in and fetch new cows to the robots several times a day to ensure they are milked, get their feed and figure everything out,” Lorusso noted. It can take seven to 10 days for cows to acclimate to the self-milking system, but many adapt quickly.
He sees the time spent training the young stock as a good investment. “Selecting cows with the most lactations in front of them and ensuring they have ideal udder placement and teat size does help everything go smoothly.” If cattle are rejected by the robot or are continually kicking while being milked, they are placed in the other barn. “There are very few problems,” Rossiter explained. “Most of the cows adapt well, but larger teats can be an issue.”
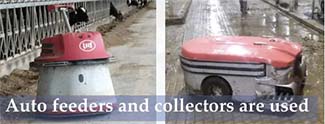
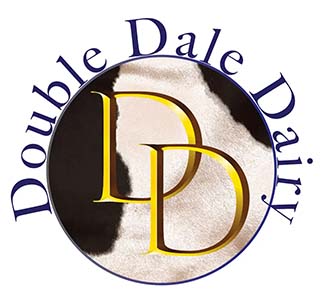
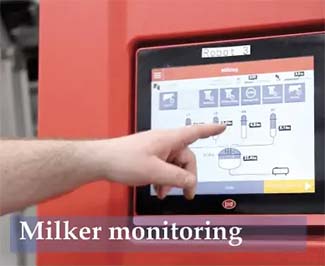
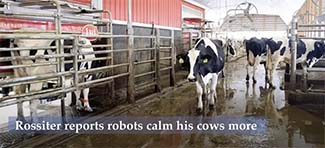
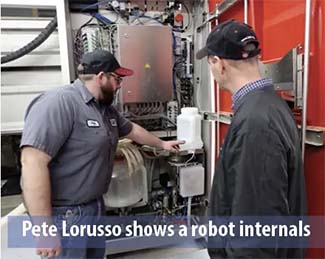
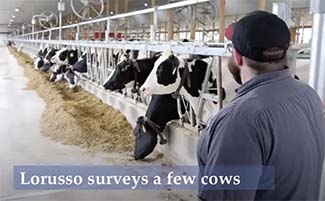
The robotic milkers do require daily cleaning and some maintenance, but Lorusso believes they require about the same amount of labor as traditional systems. However, the actual tasks are a bit different. “It takes more time for the people to get comfortable with everything than it does for the cows.”
In addition to the robotic milkers in the new barn, there are also Lely Discover Collectors. The collectors don’t scrape manure; they vacuum up the manure. These collectors spray water from the front and back ensuring most of the manure is removed from the solid flooring. Able to be programmed to meet individual needs, the new Double Dale barn is using eight collectors that are active 24 hours a day. “These Lely Collectors do a phenomenal job,” Lorusso commented.
All the cows are artificially inseminated. Bull calves are sold at a couple of days old, and heifer calves are raised on-site. The newborn heifer calves are housed individually and bottle-fed for 10 to 14 days before being moved to group housing and an automated feeding system.
Dairy farming has been a constant in United States since the 1600s when families immigrated from Europe. Family dairies are no strangers to the struggles brought on by changes in economics and regulations. The key to survival for Double Dale Dairy has been a reliable cow herd, great employees, partnering with National Famers, a passion for dairy farming and embracing technology.
“People need to embrace technology that is beneficial to our dairy industry and other agriculture sectors and then teach others,” Rossiter said. Nearly three years into the new barn utilizing the Lely robotic system, everyone is pleased with the change.
Yes, it took longer for the people to adapt than it did for the cattle, but cows always come first on dairies.
Lorusso summed up the conversation with this thought – “With four times the data being collected in the new barn, we can monitor the cows closely ensuring our product is top quality and our cows are happy,”